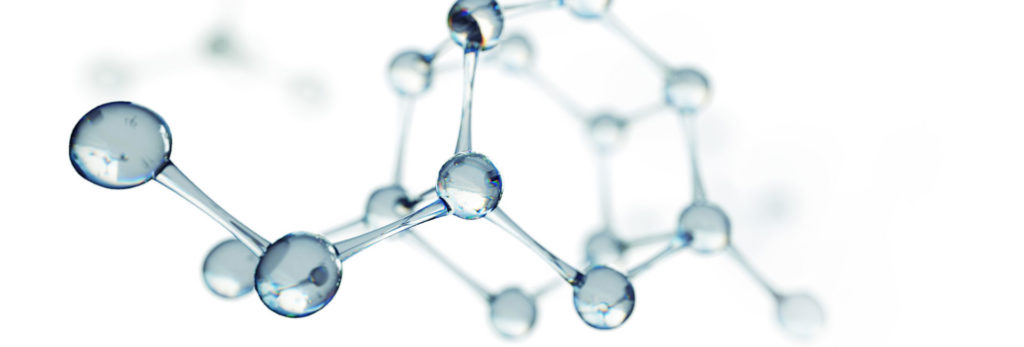
REE SEPARATION
Rare Earth Elements (REE) separation is the third and the final step in making REE compounds from mineral ore. REE invariably occur together in nature and therefore any given REE mineral will contain several or most of the 17 REE in variable quantities. Consequently, when a rare earth concentrate (REC) is produced, a mixture of REE is present that needs to be further refined into their individual elements, whether in their oxide or metal form, before they can be applied in their various end products.
To get to a REC, the first step is beneficiation where the natural REE-bearing minerals disseminated through the ore are liberated by crushing and grinding followed by concentration through flotation, magnetism and other means based on their physical properties. The second step is hydrometallurgy, a processing method in which the mineral concentrate resulting from the beneficiation is broken down, using thermal and chemical agents. Although hydrometallurgy varies from project to project, depending on the REE mineral in question, both steps are relatively simple and quite achievable through conventional methods. Nevertheless, it comes down to cost, scale, environmental regulations, infrastructure and permitting when choosing the optimal combination of beneficiation and hydrometallurgy for any project.
Both these steps have only a limited capability to differentiate between the individual REE and are often done at the expense of significant overall recoveries.The reason being is that the chemical properties of REE do not deviate significantly from one another. Consequently, purification and separation of individual REE today is tremendously tedious and requires several processes with the majority of the world’s REE processing facilities today located in China. A REE refinery often includes many consecutive steps, each resulting in minute improvement in the complex REE stream with the overall processing cycle taking a great deal of time.
CURRENT SEPARATION
Today, countercurrent solvent extraction is generally accepted as the most appropriate commercial technology for separating rare earths. The key step in the extraction process is the selection of a suitable solvent combined with a suitable extraction condition. Effective extraction and separation is unlikely to be achieved in a single step, and it is therefore necessary to prepare an aqueous solution containing the REE and extract this solution repeatedly with an organic solvent. This makes the acid and the base the main consumables in the solvent extraction process, and the spent REE acidic solution becomes one of the main pollution sources. Using this method, a plant producing multiple single rare earth products may contain hundreds of stages of mixers and settlers. As a result, many separation stages are typically needed to obtain a pure product.
Inherent aspects of the solvent extraction technique:
- Large amount of organic and inorganic solvents in the process flow sheet
- Chemical adjustment based on REE distribution of concentrate
- High capital cost chemical facilities
Scientific reading on solvent extraction:
- A critical review on solvent extraction of rare earths from aqueous solutions (Xieet al. 2004)
- An introduction to some aspects of solvent extraction chemistry in hydrometallurgy (Hudson 1982)
- Extractive metallurgy of rare earths (Gupta and Krishnamurthy 2004)
- Solvent extraction in China (Zhu 1991)
- Solvent extraction used in industrial separation of rare earths (Brown and Sherrington 1979)
The following 4 investigative reports explain the dominance of China in the industry, the difficulties with rare earths mining, its environmental impacts and its impacts on our day to day lives:
- Costing The Earth – Rare Earth Investigation report by CCTV News on the polluting nature of mining and processing rare earth elements in China using current methods.
- Modern Life’s Devices under China’s Grip?: A report by CBS News 60 Minutes on the REE market, demands, Chinese environmental problems and China’s dominance in the sector.
- The dystopian lake filled by the world’s tech lust: A report by BBC on the Bayan Obo mines in China.
- What on earth are rare earths and where can you find them? An explainer: An article by Financial Post on rare earths, their uses and their complex supply