Bauxite Residues Processing
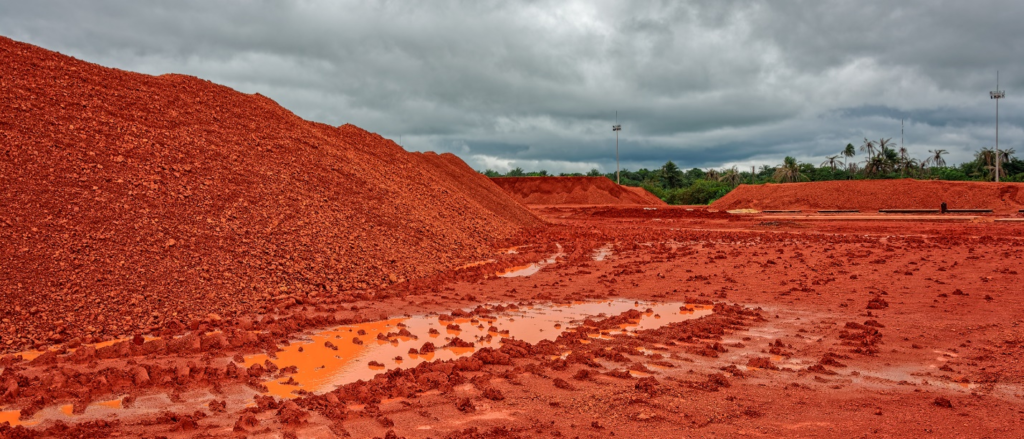
Bauxite residues is the largest waste by-product generated in the Bayer bauxite refining alumina production process. Large quantities of this caustic red mud are generated worldwide every year, posing environmental and safety challenges. Storage of bauxite residues is a challenge for alumina refineries with over 80 plants across the world currently producing alumina from bauxite ore. It is estimated that over 1.4 tonnes of bauxite residues is generated per tonne of alumina produced and as the demand for aluminum metal increases so does the production of bauxite residues. As a result of population growth, many of these plants are now located inside urban areas resulting in storage space limitations and increasing environmental regulations that threaten these operations. Closure of these alumina refineries could result in the loss of thousands of jobs and millions of dollars of economic benefits for these regions.
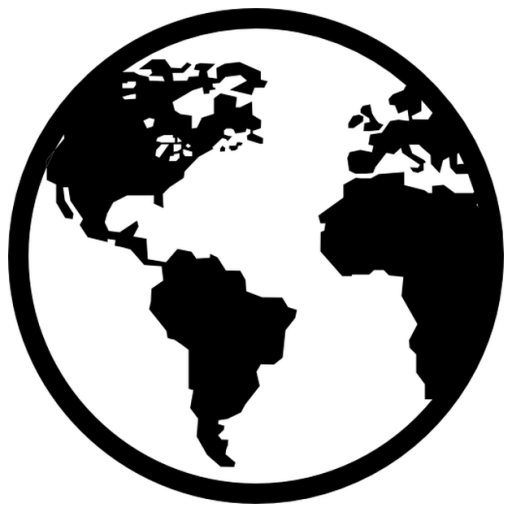
More than 80 plants worldwide produce bauxite residues
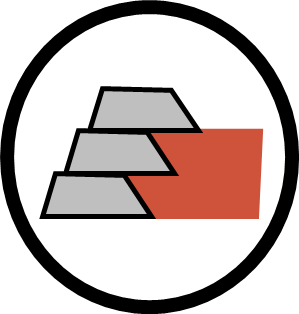
Over 4 B tonnes of Bauxite Residues are stored in tailings globally
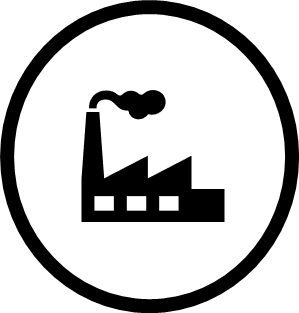
Over 150 M tonnes of Bauxite Residues are produced annually worldwide

$80 – $120 in lost metal value per tonne of bauxite residues
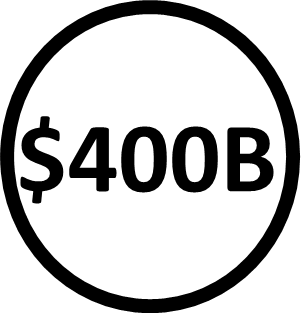
>$400B in metal value in storage
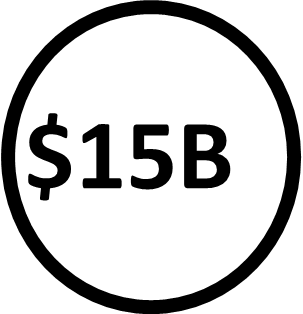
>$15B in metal value in annual bauxite residues production
Bauxite residues pose significant environmental risks due to its large volumes, high alkalinity and storage complications with risk of groundwater and nearby ecosystems contamination. Globally, the CAPEX and OPEX costs of bauxite residues disposal are estimated at between $4 and $8/tonne. On the other hand, based on its global average composition, the lost metal value is estimated between $80 and $120/tonne.
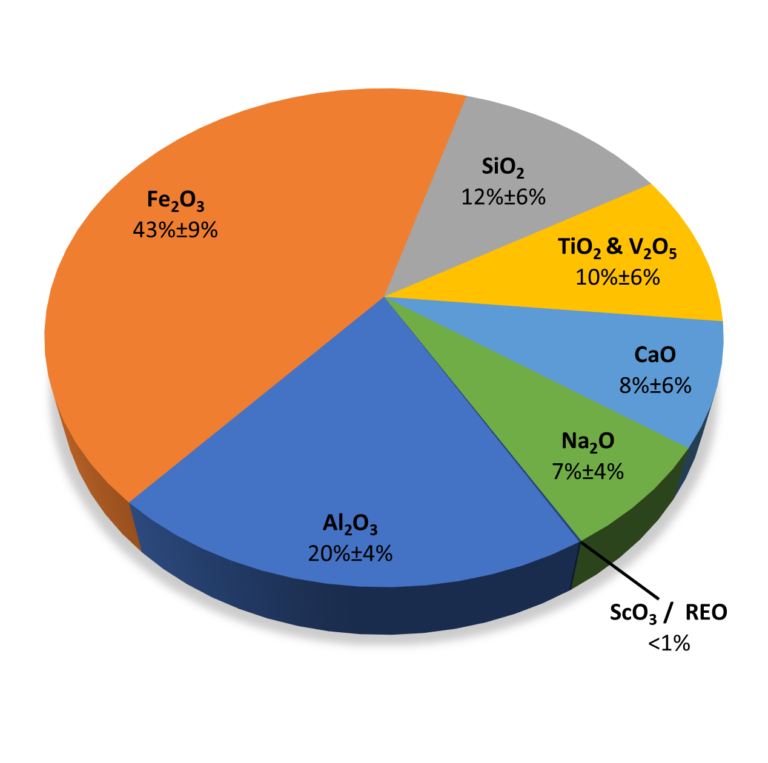
Bauxite Residues Average Composition
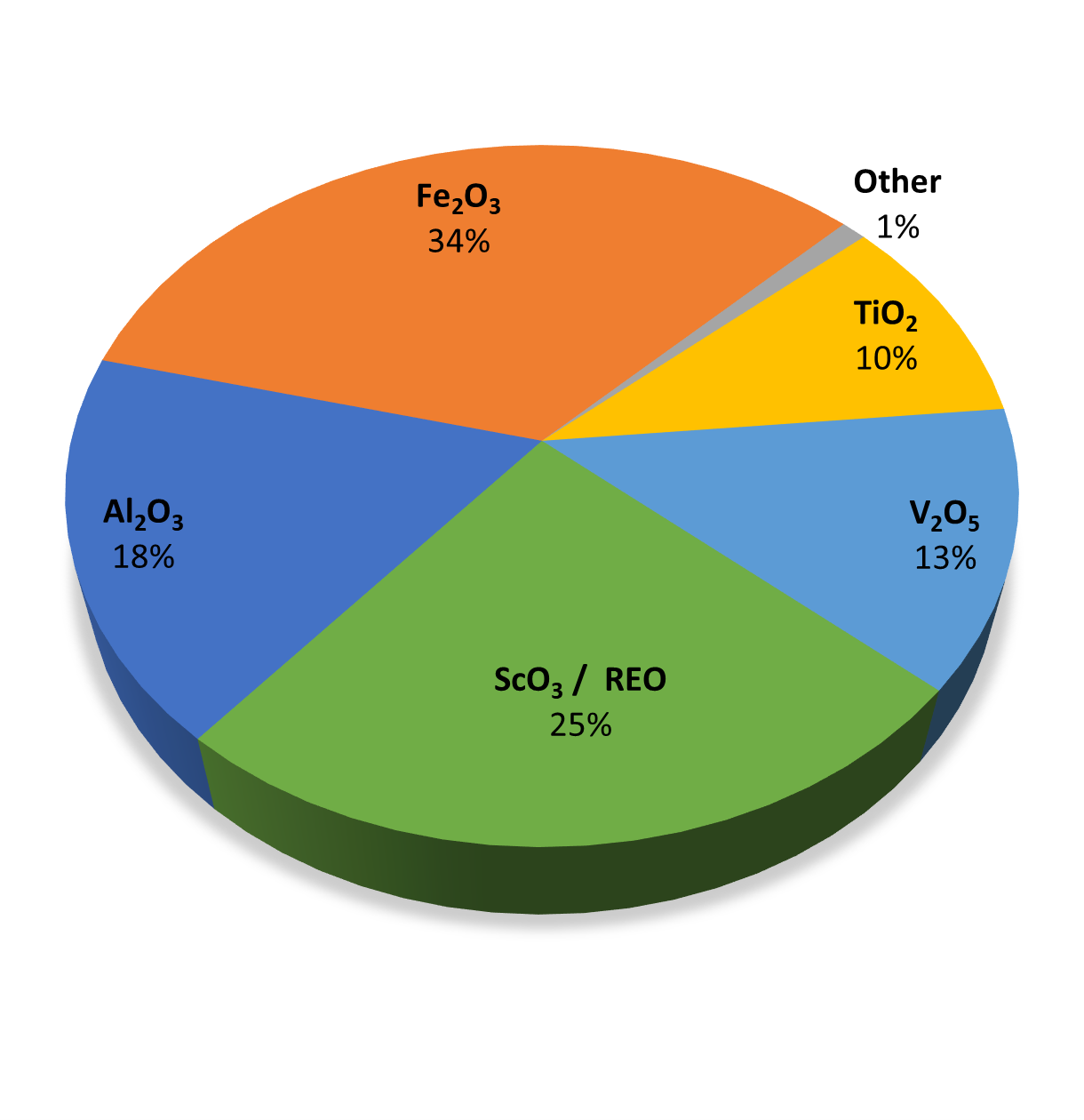
Bauxite Residues Value Distribution
In Canada, it is estimated that 1.5MT of bauxite residues are produced annually and 40MT are accumulated in storage sites that take up approximately 2.2km2 of valuable urban land space.
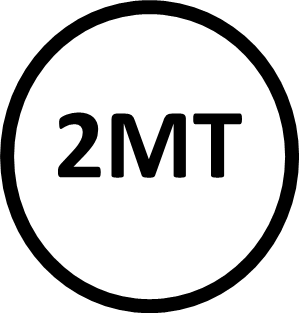
An average plant will produce around 2MT of bauxite residues per year
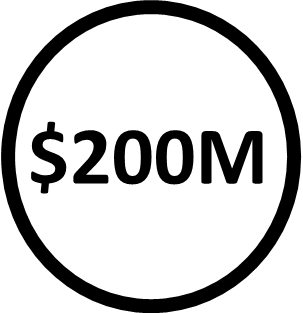
$200M in metal value per year mostly in Iron, Aluminum and Scandium
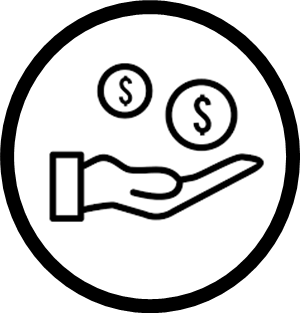
Technology to be deployed globally through licensing and royalty agreements
Currently, less than 5% of bauxite residues are being reused but due to past environmental incidents, the International Aluminium Institute (IAI) set a goal to reuse 25% of bauxite residues by 2025. The technology developed by Geomega’s R&D subsidiary Innord is targeting approximately 80% reuse, significantly higher than the IAI target.
Eliminating or significantly reducing the bauxite residues storage sites would extend the lifespan of the existing plants, help maintain jobs in the alumina refining industry that is under pressure to improve its environmental footprint and create new jobs associated with the new bauxite residues processing industry.
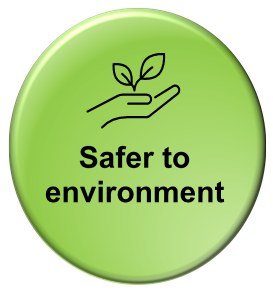

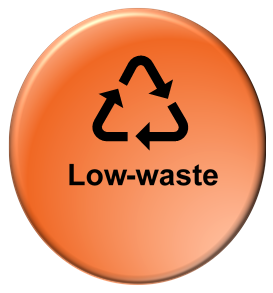
Geomega is not the first company to try processing bauxite residues. Over several decades, many research institutions and companies have tried various chemical processes but with major shortcomings such as:
- Environmental impacts are displaced towards other effluents and emissions
- Not effective enough in reducing the waste volume
- Not economically viable: high reagent and energy consumption
The hydrometallurgical process developed by Innord, addresses these issues:
- Recovery of bulk metals (Fe, Al) to maximize volume reduction (>80%)
- Production of valuable minor metals concentrates (Ti, V, Sc/REE)
- Recycling of main reagents to reduce costs and effluents
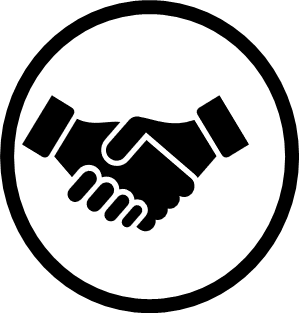
Geomega is working with a major international industrial partner to advance its technology to the piloting stage. Ownership of the Intellectual Property developed by Innord through this research work will remain with Innord. With bauxite residues representing a global challenge, Innord is developing the technology with the objective to make it available globally. Based on its successful scale up, a licensing and royalty agreement will be established which will be the basis for a rollout of the technology.
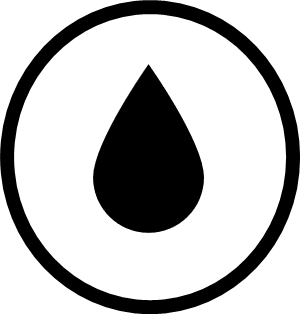
To conserve water and contribute to cleaner water
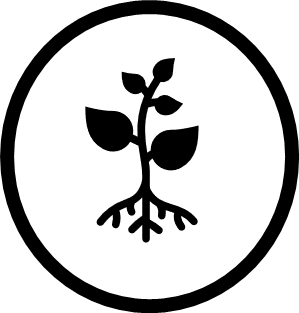
To remove potential of soil contamination from seepages
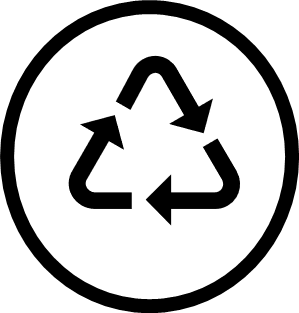
Recycling of main reagents and production of various metals without additional primary mining
An alternative to bauxite residues storage will result in cleaner water and soil by avoiding seepage of exotic elements and recovery of bulk metal components in the form of sellable concentrates allowing to reduce the volume of solid waste. By recycling the main reagents and solvents, water is conserved and environmental impacts are not displaced to other types of effluents. Furthermore, the process also contributes indirectly to climate change by producing metals such as Scandium (Sc) and Aluminum (Al) used to manufacture light and fuel-efficient vehicles and also avoiding the Green House Gasses (GHG) emissions from the primary production of these recycled materials.
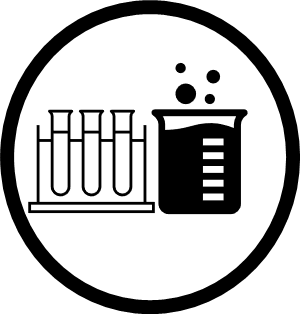
The testwork already completed by Innord successfully demonstrated the process on bench scale with the main units of operation including alkalinity removal, recycling of reagents and solvents and recovery of various metal streams. These results led to an internal positive economic evaluation which is the basis of the currently ongoing testwork and modeling in preparation to pilot testing of the technology.
Innord’s bauxite residues processing flowsheet is based on a combination of several metallurgical routes and proprietary techniques already designed and optimized by Geomega in other projects such as iron recovery, reagents recovery and REE extraction and purification. The technology benefits from various innovation factors which have an important effect on the price and its performance:
- Synergistic effect of processing steps to facilitate isolation of different bulk metals
- Rare earths extraction from a non primary mining source and recovery of high value Scandium
- Recycling of main reagents affects significantly the environmental impact and operating cost
- The reagents are not corrosive which eliminates the need for high-cost specialized equipment
- The recovery of multiple valuable concentrates sellable to specialized metal producers improves profitability
- Sophisticated purification steps (e.g., SX, electrolysis) are avoided which reduces CAPEX and de-risks scale-up
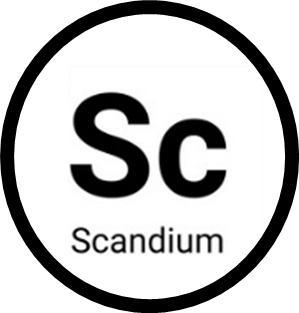
The Scandium factor is of particular interest with bauxite residues processing. Small quantities of Scandium are used to improve the tensile strength and physical properties of aluminum. Aluminum-Scandium alloys (Al-Sc alloys) are growing in interest from the automotive, aerospace, oil and gas and many other industries but its lack of supply keeps the price too high for most commercial applications. Furthermore, limited supply diversification with Sc mainly produced in Russia and China, prevents many industries from committing to Al-Sc alloys in a significant way. Sc content in bauxite residues varies depending on the bauxite source with up to 120 g/t of Sc reported (equivalent to 240 tpy of ScO3 in an average alumina refinery).